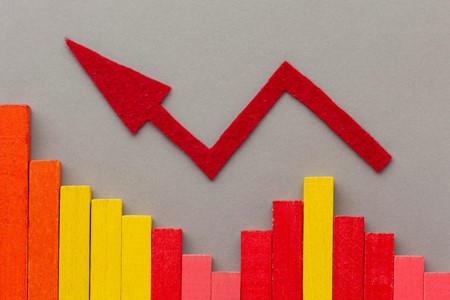
In the dynamic landscape of the chemical industry, the pricing of raw materials plays a pivotal role in determining the overall cost structure and competitiveness of chemical products. Raw material costs can fluctuate significantly due to a myriad of interconnected factors, each exerting its influence on the supply chain. Understanding these factors is essential for industry stakeholders, from manufacturers to investors, as they navigate the complexities of the global market. By examining the key determinants, we can gain a comprehensive understanding of the challenges and opportunities that characterize the procurement and utilization of raw materials within this vital industry.
Supply and Demand
Supply : The price of raw materials can fluctuate due to production limits, logistical challenges such as increase in freight charges due to port congestion, transportation strikes. An example for logistical challenge: An Indian company, ABC, wants to import acetic acid from China. Initially, the ex-works price is 400 USD per ton, but due to port congestion, the CIF price quoted is 600 USD per ton, with freight costs at 200 USD. ABC delays its order and checks again after 15-20 days, finding the freight cost reduced to 120 USD per ton. This fluctuation in freight charges significantly impacts the raw material cost. Additionally, choosing the right shipping company can also affect overall expenses.
Demand : When the demand for a raw material exceeds its supply, prices naturally increase. The balance between supply and demand is a fundamental factor driving price fluctuations in the chemical industry. During the COVID-19 pandemic, the demand for disinfectants, which require ethanol as a key raw material, surged, leading to a significant increase in ethanol prices.
Economic Conditions
Global Economy : Economic health globally impacts raw material prices. A strong economy can increase demand and prices, while a recession can decrease them. Let’s take the example of the 2008 financial crisis which led to a global recession, decreasing industrial activity and demand for raw materials, which caused prices to fall.
Exchange Rates : Raw material prices can fluctuate with changes in exchange rates. For example, if the USD to INR rate is 83-84, importing oxalic acid at 500 USD per ton costs Rs. 42,000. If the rate drops to Rs. 80, the price decreases to Rs. 40,000 per ton, saving Rs. 2,000 due to exchange rate fluctuations. Thus, day-to-day exchange rate changes impact raw material costs.
Energy costs
The costs of energy, particularly oil and gas, plays a significant role in the production and transportation of raw materials. High energy costs can drive up prices.
Speculation and market sentiments
Market speculation and investor sentiment can cause price volatility. Speculative trading in commodities and raw materials can lead to rapid price changes, reflecting market perceptions rather than fundamental supply and demand dynamics.
Production Capacity
Plant Capacity and Utilization Rates: The operating capacity of chemical plants and their utilization rates influence the availability of raw materials. Overcapacity can lead to lower prices, while undercapacity or shutdowns can lead to higher prices. In 2017, Hurricane Harvey caused several chemical plants in Texas to shut down, reducing the production capacity of ethylene, a key raw material. This disruption led to a spike in ethylene prices due to decreased supply.
Natural Events
Natural disasters such as hurricanes, earthquakes, and floods can disrupt the supply chain, affecting the availability and cost of raw materials. These events can cause immediate and significant impacts on production and logistics, leading to price spikes. For e.g. The 2011 earthquake and tsunami in Japan disrupted the production of several key chemicals and raw materials, leading to increased prices due to supply chain disruptions.
Geopolitical Issues
Conflicts, political instability, and changes in government policies in key producing regions can impact the supply and cost of raw materials. Geopolitical tensions can lead to supply disruptions, trade restrictions, and increased costs, all of which can influence raw material prices in the chemical industry.
Disclaimer – Please note that the prices of the raw material mentioned in the examples given above are illustrative and does not indicate actual prices.